FFC vs FPC: Understanding Flexible Cable Technologies
Flat Flexible Cables (FFCs) and Flexible Printed Circuits (FPCs) are two types of flexible cables commonly used to connect devices together when working with electronics. As flexible cables, both are built to easily make connections with more flexibility than traditional rigid cables. FFCs and FPCs are often confused based on their similar appearance, but both serve different purposes and are better suited for certain projects.
In questo articolo:
FFCs: Flat Flexible Cables
Flat Flexible Cables (FFCs) are a type of flexible cable that provide a 1:1 connection between devices. They consist of multiple flat wires placed parallel to each other and covered with a protective shielding tape. This makes these cables a great option for projects that require quick connections or high-flex applications where the cable needs to bend repeatedly without breaking.
Types of FFCs:
There are two main types of FFCs, each of which has a different layout of contacts, or pins. Both types can be referred to by a variety of names, but they’re most commonly known as Type A and Type D.
- Type A (also known as Type 1, Type BD, or Same Side): Each end of the cable is lined with a row of pins, both of which lie on the same side of the FFC’s surface. This is the most commonly used type of FFC.
- Type D (also known as Type 2, Type AD, or Opposite Side): Each end of the cable is lined with a row of pins, one of which lies on the top side of the FFC and the other on the bottom side. This type of FFC is less common and is typically used in special-case applications, for example, to connect a device that has a standard pin layout to a device that has a reverse-order pin layout.
Related: Touchscreen Types & How they Work
Parts of an FFC:
- Wires: Flat conductive paths that carry electrical signals between the devices that the FFC is connected to.
- Pins: Individual conductive contact points at each end of an FPC that connect to corresponding pins on another device.
- Pitch: The distance between the centers of two adjacent pins. The pitch size determines the cable's compatibility with connectors.
- Support tape: Reinforcing layers added to ends of the FFC to make it easier to insert into a connector without damage.
What FFCs are Made of
FFCs are made of a row of flat wires composed of copper and plated in tin at each end. A flexible polyester material is covered around the row of wires to insulate and protect the conductors. At each end of the cable are rectangular stiffeners, which are typically made of a thicker polyester material.
How FFCs Work
FFCs are designed to connect to a device at each end through a 1:1 connection, meaning that each pin on one end of the FFC corresponds exactly to the same number pin on the device it’s being connected to. Once an FFC is properly connected to a device at each end, electrical signals are able to travel from one device through the conductors of the FFC to reach the other device. This connection allows the two devices to communicate while they’re connected with the FFC and a power source.
Related: How to Connect LCD to Arduino
Advantages of FFCs:
- High flexibility: The flexible materials that FFCs are composed of make them suitable for applications requiring frequent movement.
- Quick setup: The simple process behind setting up an FFC between devices allows for quick connecting and disconnecting.
- High versatility: The function of an FFC is to create a 1:1 connection between devices, which means the cable can easily be reused in any other projects that require a 1:1 connection.
- Cost-effective: FFCs generally cost less to produce than FPCs, so they can be bought at a lower cost.
Disadvantages of FFCs:
- Limited complexity: FFCs cannot support the same level of circuit complexity as FPCs, so they are not well suited for advanced functionality requirements.
- Durability: FFCs may be less durable than FPCs in harsh environments.
Common Uses of FFCs:
- Cameras: In cameras, FFCs connect the image sensor with the processing board to transmit high-resolution image data.
- Robotics: FFCs are often used in moving robotic parts like robotic arms, making up flexible joints and allowing for a wide range of motion.
- Consumer electronics: FFCs are used to connect components within everyday devices such as laptops, printers, and monitors.
- Automotive: Dashboards, infotainment systems, and other in-car electronics use FFCs to make simple connections within the system.
- Medical devices: FFCs are incorporated into imaging equipment and diagnostic machines used within medical spaces.
- Industrial equipment: Industrial robotics and automation systems utilize FFCs to connect many components throughout the machinery.
- Home appliances: FFCs are utilized across household appliances like washing machines, microwaves, and other household devices.
Example FFC project: Using Gameduino 2 Library with EVE2 TFT Modules
FPCs: Flexible Printed Circuits
Flexible Printed Circuits (FPCs) are a type of flexible cable that allows circuits to be printed onto a flexible substrate. These flexible printed circuit cables can bend and fold, allowing for complex electronic connections in confined spaces. FPCs perform the same functions as traditional Printed Circuit Boards (PCBs) but on a flexible surface.
Printed atop an FPC is a highly customizable circuit, so each FPC is typically designed to be used for a specific application. Their flexible and lightweight build makes them best for projects that require a more complex connection within a limited space.
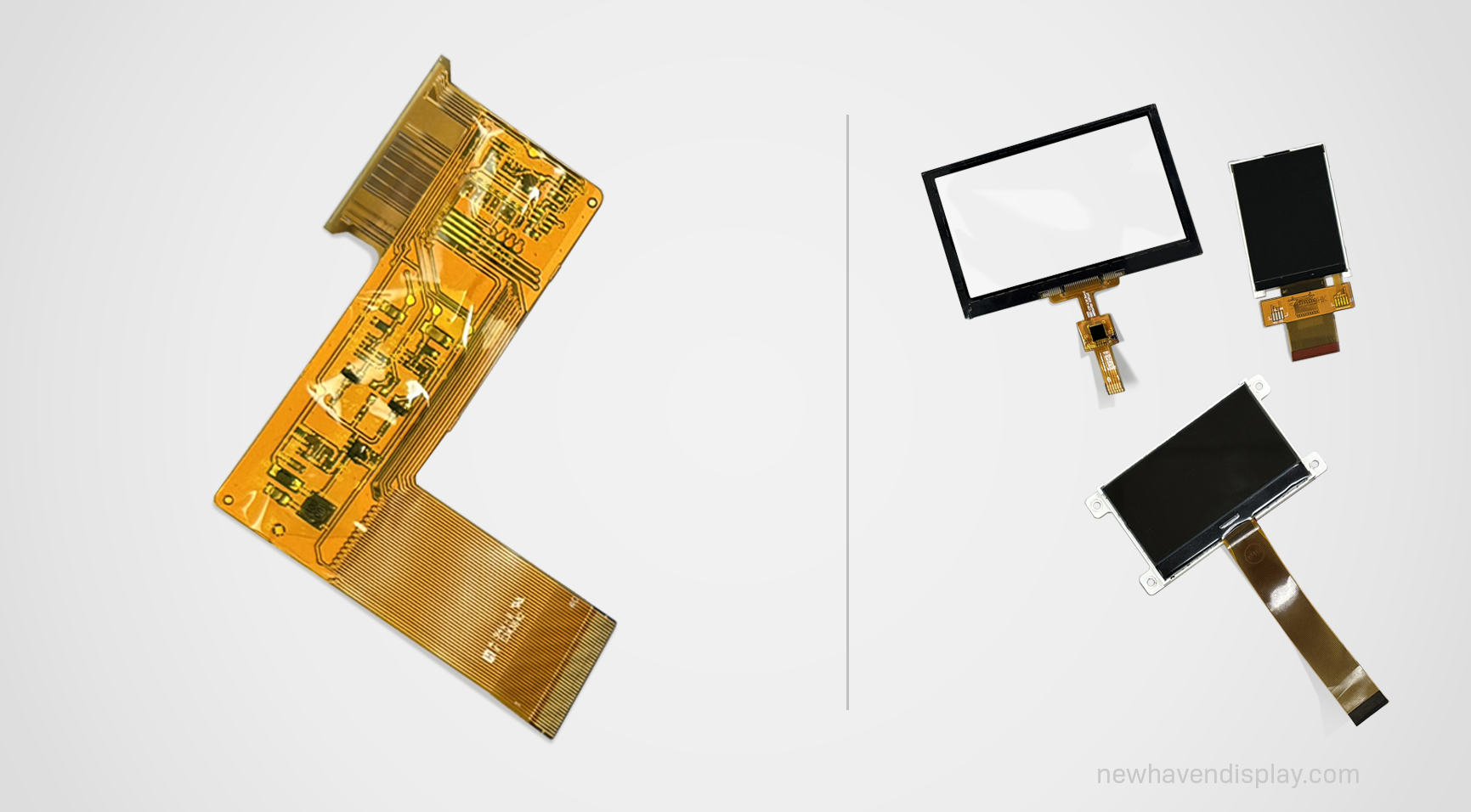
Parts of an FPC:
- Pins: Individual conductive contact points at each end of an FPC that connect to corresponding pins on another device.
- Pin out: The arrangement of pins on an FPC. The pin out ensures correct alignment for transferring signals.
- Pitch: The distance between the centers of two adjacent pins. The pitch determines the cable's compatibility with connectors.
- Through-hole: Plated holes that allow electrical connections between different layers of the FPC.
- Electrical traces: Pathways that carry electrical signals across the FPC. FPCs can consist of one layer or multiple layers of conductive traces.
- Electrical components: Various devices mounted onto an FPC, including resistors, capacitors, integrated circuits, and transistors.
- Stiffener: Rigid pieces added to certain areas of the FPC to provide additional support, especially at connection points.
- Substrate: The base material of the FPC, which provides the flexibility and support for the conductive traces.
What FPCs are Made of
FPCs are built starting with a flexible base layer made from polyimide or polyester. Atop this base, one or more layers of conductive traces made from copper are bonded down using an acrylic or epoxy-based adhesive above each layer. Multi-layered FPCs have through-hole vias coated with copper along the inside and ends of the hole to allow the layers to interact.
Throughout the FPC, thin polyimide-based stiffeners or thicker stiffeners made of fiberglass-reinforced epoxy may be used in certain areas to provide varying levels of additional support.
Overtop all, a polyimide coverlay provides an insulating and protective layer. FPCs may also come with a shielding layer made of aluminum or copper foil over parts of the cable to prevent EMI. Tin or gold-plated pins lay at each end of the cable for easy solderability.
How FPCs Work
Similar to an FFC, each end of an FPC has an array of pins that connect to a different device on each side. When connected to a power source, this allows the two devices to communicate with each other by sending electrical signals from one device through the FPC to reach the other device.
Unlike an FFC, the electrical signals travel through the FPC on more complex paths, following the traces etched onto the FPC. Some signals will also travel directly to certain mounted components, rather than passing straight through to reach the device at the other end. In multi-layered FPCs, each layer of traces is separated, so a signal can reach other layers by traveling through the conductive exterior of the through-hole.
Related: How Image Burn-In Works
Advantages of FPCs:
- High complexity: FPCs are able to support complex circuit designs, including multi-layer and surface-mount components.
- High customization: With the capacity to incorporate countless versions of circuit designs in multiple layers and attach additional components, FPCs can be highly customized to serve specific functions for niche applications.
- High flexibility: The flexible material that acts as the base for the cable allows FPCs to perform well in applications that require frequent movement.
- Strong durability: FPCs are typically more resistant than FFCs to harsh conditions, like high temperatures and exposure to chemicals.
Disadvantages of FPCs:
- Higher cost: Due to their complex designs, FPCs require more materials and time to produce, making them typically more expensive than FFCs.
- Limited reusability: The circuits within each FPC are designed for specific purposes, so they can only be reused in projects that require the same functionality out of it.
- High design complexity: Compiling FPCs with advanced circuit patterns may take an extended time to complete.
Common Uses of FPCs:
- Smart watches: Due to their flexible build and advanced capabilities, FPCs are used in smart watches for functions like processing live health statistics collected from a sensor.
- Satellite solar panels: Inside satellites deployed to outer space, FPCs are used to connect the solar panels to the satellite's power management system. Light in weight, it helps to avoid excess fuel usage caused by additional weight.
- Consumer electronics: FPCs can be found in smartphones, tablets, laptops, and cameras, where space constraints and flexibility are crucial.
- Automotive: FPCs are used within complex automotive parts and systems like dashboard controls, infotainment systems, and advanced driver-assistance systems (ADAS).
- Medical devices: In the medical field, FPCs are found in diagnostic equipment, wearable health monitors, and imaging systems.
- Aerospace and defense: Due to their lightweight build, FPCs are incorporated within aerospace navigation systems, communication devices, and control panels.
- Industrial equipment: FPCs are commonly used within advanced equipment in areas like robotics, automation systems, and complex machinery.
Differences Between FFCs and FPCs
FFCs and FPCs are both types of flexible cables. The main difference is that FFCs contain basic wires, suitable for simple connections. On the other hand, FPCs are like miniature circuit boards on a flexible sheet, enabling complex connections and additional functions for space-saving applications.
FFC vs FPC vs Rigid Cable Comparison Table:
FFC | FPC | Rigid Cable | |
---|---|---|---|
Complexity of functions | Low | High | High |
Customization | Low | High | Low |
Thickness | Very thin | Thin (varies) | Thick |
Overall size | Small | Small (varies) | Large |
Weight | Light | Light | Heavy |
Durata | Moderate | High | Varies |
Costo | Low | Moderate | High |
Common uses |
|
|
|
Advantages | Easy to use, affordable | Flexible, complex functionality | Robust, durable |
Disadvantages | Limited functionality | Higher cost | Bulky, low flexibility |
Related: Nits vs Lumens vs Luminance
Choosing Between an FFC and FPC
When choosing between an FFC and an FPC for a project, it's important to consider the factors below about your project before deciding which flexible cable to use.
Complexity of functions
- FFC: Suitable for making simpler connections where high flexibility is needed, but the circuit does not require intricate routing.
- FPC: Ideal for performing functions that require complex circuit designs with intricate routing, multiple layers, or additional electrical components.
Movement
- FFC: Excellent for applications requiring frequent bending.
- FPC: Suitable for applications where the circuit must fit into tight or irregular-shaped spaces and endure dynamic movements.
Budget
- FFC: Generally more cost-effective due to their simpler design.
- FPC: More expensive due to the design complexity and required materials.
Environmental conditions
- FFC: Typically used in environments with moderate thermal stress. Polyester-based FFCs can handle standard conditions, but polyimide-based FFCs offer better thermal stability.
- FPC: Well suited for standard or harsh environments, including high temperatures, chemical exposure, and mechanical stress.
Space constraints
- FFC: Suitable for applications where space is limited, but the flexibility of the routing is relatively straightforward.
- FPC: Excellent for tight spaces due to their ability to conform to various shapes and sizes.
Conclusione
FFCs and FPCs are both made to connect together devices in projects that require a flexible, bendable cable. Past this, each cable has strengths that better suit different applications. FFCs are best for applications that require quick, straightforward 1:1 connections, whereas FPCs are best for those that require more complex and specific functionality.
Ultimi post del blog
-
OEM vs ODM Manufacturing - Differences, Benefits, and Limitations
When outsourcing manufacturing, two terms come across: OEM (Original Equipment Manufacturer) and …Nov 26th 2024 -
Raspberry Pi Custom HDMI TFT LCD Timings
Setting up custom timing for HDMI TFTs and Touch HDMI Displays on Raspberry Pi can significant …Oct 29th 2024 -
Arduino vs Raspberry Pi: Key Features and Differences
If you're working on an electronics project—whether it's for a DIY automated device, a digital si …Sep 4th 2024